I wanted to tune the Greddy Type-S BOV on the 1.8T project. Here are the things I did, accomplished and learned from BOV tuning on the 1.8T. The car has a Greddy Type-S but the principle should be the same for any blow-off valve.
BOV Setup – Key Takeaways
- Before adjusting the BOV, make sure all the lines are not leaking vac/boost. Don’t make the mistake I made…
- We want the springs in the BOV to be at the softest possible setting so boost can be released as easily as possible and as fast as possible.
- For a recirculating BOV, I believe it’s no problem if the valve opens at idle.
- For a BOV dumping to atmosphere it’s preferable for it to be closed at idle, although I don’t see any reason why this couldn’t be compensated for in the tune eg for X inlet manifold vac and X RPM output a fixed MAF signal to the ECU/auto tune using the AFRs at idle.
Why Adjust the BOV?
When lifting off the throttle there would be a fluttering sound coming from the intake. Some call this wastegate flutter but I think in most cases the “tsooo-tsooo-tsooo” sound is actually compressor stall/compressor surge.
When the throttle is closed the pressurised air has nowhere to go and backs up through the intake system until it hits the compressor wheel of the turbo, and this is what causes the “flutter” noise.
So What?
A couple of big issues with compressor stall.
The first is the stress on the turbo bearing. The air coming back from the throttle body pushes the compressor wheel towards the turbine putting stress of the turbo bearings. On a ball bearing turbo not such a big deal with on non-ball bearing turbos, there can be wear.
The other issue is the stalling of the compressor wheel. When the throttle is reapplied, it’s going to take some time for the turbo to spin up to speed again. This makes the car slower, which is obviously a problem.
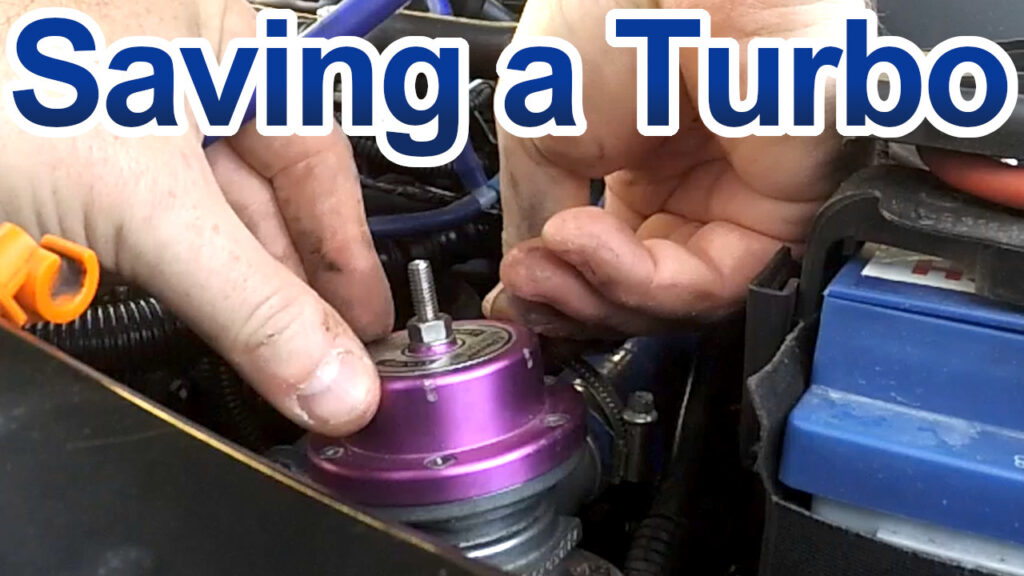
BOV Tuning
Which brings me back to the purpose of tuning the BOV (dump valve), recirculating in the case of the 1.8T project but also applies to BOVs venting to atmosphere.
The fluttering the car was making was slowing down the turbo between gear changes and when lifting the throttle. And I wanted to stop this. And also reduce the stress on the turbo bearings, in the case of the K04-064, journal bearings.
What I Did
First port of call from me was to adjust the compression of the springs in the BOV. The Octavia RS is running a Greddy Type-S BOV. Reducing the compression on the springs was a matter of turning ther adjustment rod outwards. I did this until it was almost out.
Unfortunately, this made absolutely no difference to the fluttering.
Next step was to open the valve and check the diaphragm was not leaking. It wasn’t. So with this, I decided to remove one of the springs to make it easier for the valve to open. There are two springs in the Greddy BOV, I removed the stiffer one, leaving the single weaker spring inside.
And again, absolutely no difference to the fluttering.
This didn’t seem right to me. The valve was so much easier to open, I thought something else must be wrong.
I unplugged the vacuum hose going to the top of the BOV to check it had vacuum. And it didn’t….
What I Should Have Started With
No vacuum to the Greddy Type-S BOV at idle was an obvious sign we had a plumbing problem and sure enough, the hose was broken at the N249 valve.
While I was in there I spotted more broken hoses but that will be for a future article.
The simple (and temporary) solution was to disconnect the N249 valve from the inlet manifold and connect the top of the BOV directly to the N249 port on the inlet manifold.
Mission Accomplished
With the BOV getting a vacuum source all the fluttering disappeared. Less stress of the turbo bearings and more response. Getting back on the throttle after a gear change the engine is ready to give the power, whereas before there was a slight delay, maybe a second.
All-in-all a huge win all round. The only negative is the “cool” sound between shifts and lifting off the throttle is gone. But I think the benefits outweigh the negative.
BOV Tuning – Key Takeaways
Before tuning a BOV in the quest to fix issues, I think it’s important to first check all hoses are in good condition ie not leaking.
Second. Check the BOV itself, is the diaphragm okay, etc.
Assuming everything is working as it should, then we can turn our attention to adjusting the spring pressure and springs in the BOV to get the results we want.
In the case of a recirculating BOV, we want the BOV to hold boost pressure to redline (although, if the plumbing is set up properly this should be no problem, if the BOV is not holding boost it’s most likely a plumbing issue with the vac lines) and we don’t want compressor stall and choo-choo noises between shifts ie we don’t want the BOV so stiff that it can open when the throttle is closed.
In the case of a BOV dumping to atmosphere, one extra thing we want is to have the valve closed at idle. (Unless we have a map to compensate for it venting).
Greddy Type-S BOV Tuning – The End Result
The BOV on the 1.8T project started with maximum spring compression and both springs.
By tuning the BOV we ended up with the single weakest spring in the BOV and set to minimum compression.
Originally the BOV was set up in a way that was the hardest it could be to open.
And we ended with a setup where the valve is setup to be the easiest it can possibly be to open, and the BOV can still hold boost (1.5 BAR) with zero issues.
This potentially makes the engine run safer & more reliably because the BOV can open faster and potentially more fully when it needs to relieve boost pressure.